Manufacturing Capacity Planning – How to Plan Production in 2024
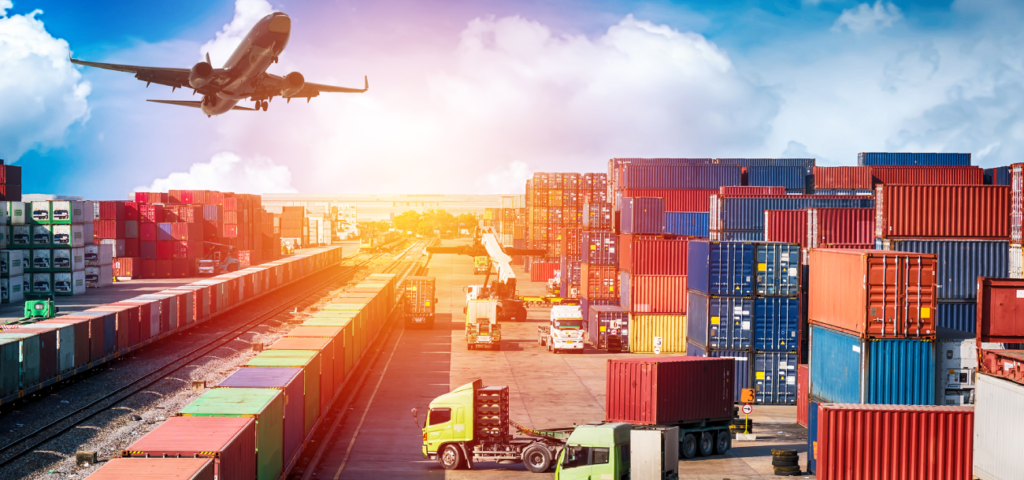
Without a solid grasp of capacity planning, manufacturers risk issues such as stockouts, excess inventory, missed delivery dates, and dissatisfied customers.
If you’re unsure how to start with capacity planning or how to navigate its challenges, this guide is for you.
We’ll walk you through the essentials of manufacturing capacity planning, from understanding its benefits and developing effective capacity plans to tackling common challenges and identifying key variables that impact capacity.
Read on to discover how to transform your manufacturing operations with effective capacity planning.
What is Manufacturing Capacity Planning?
Manufacturing capacity planning is a strategic process that ensures an organization can efficiently meet its production goals and customer demands.
It involves carefully analyzing the available resources, including equipment, labor, and materials, to determine the optimal production schedule and capacity requirements.
Capacity planning aims to balance supply and demand, preventing over or underutilization of resources.
The role of capacity planning in manufacturing operations is multifaceted. It enables organizations to:
- Identify potential bottlenecks and constraints in the production process
- Allocate resources effectively to meet production targets
- Respond quickly to changes in customer demand or market conditions
- Optimize inventory levels and reduce the risk of stockouts or excess inventory
- Improve delivery times and customer satisfaction
Accurate forecasting and demand planning are crucial for effective manufacturing capacity planning. Organizations can predict future demand and adjust their production plans when they analyze historical data, market trends, and other relevant factors.
This proactive approach helps manufacturers stay ahead of the curve and maintain a competitive edge in the market.
What are the Benefits of Manufacturing Capacity Planning?
The benefits of manufacturing capacity planning are enhanced efficiency, productivity boost, and overall operational effectiveness. It also influences cost reduction, enhances customer satisfaction, and improves decision-making.
Now that we’ve covered the “what,” let’s get into more detail in the breakdown below:
Improved Efficiency and Productivity
Capacity planning ensures that manufacturing resources, such as labor, machinery, and materials, are optimally utilized.
When producing capacity is aligned with demand forecasting, companies can avoid bottlenecks and underutilization of resources, leading to smoother production processes and higher output rates.
This optimization reduces idle time and increases the overall productivity of the manufacturing operations.
Cost Reduction
Effective capacity planning helps in minimizing costs associated with overproduction and underproduction.
Companies can reduce excess inventory, lower storage costs, and avoid the expenses related to last-minute production adjustments when accurately forecasting demand and aligning production schedules accordingly.
This leads to significant cost savings and improved profitability.
Enhanced Customer Satisfaction
Capacity planning ensures that the right amount of products is available at the right time, reducing lead times and improving delivery performance.
This reliability in fulfilling customer orders enhances customer trust and loyalty, contributing to long-term business success.
Better Decision-Making
Capacity planning provides valuable data and insights that support strategic decision-making.
Companies can make informed decisions about investments in new machinery, workforce expansion, and process improvements, and capacity requirements and production capabilities are properly analyzed.
This data-driven approach helps identify potential areas for growth and optimize resource allocation.
Increased Flexibility and Agility
Capacity planning enables companies to build flexibility into their production processes, allowing them to scale up or down based on market conditions.
This agility helps the company respond to unexpected demand spikes or downturns, ensuring it remains resilient and competitive.
Improved Quality Control
Capacity planning helps maintain consistent quality standards by ensuring that production processes are well-planned and resources are adequately allocated.
Improved quality control reduces the likelihood of rushed production runs, which can lead to errors and defects.
Consistent quality control enhances the company’s overall reputation and reduces costs associated with rework and returns.
Strategic Alignment
Intelligent capacity planning also aligns production capabilities with the company’s strategic goals.
It ensures that manufacturing operations align with market demands, business objectives, and growth plans. This alignment helps achieve long-term business success and maintain a competitive edge in the market.
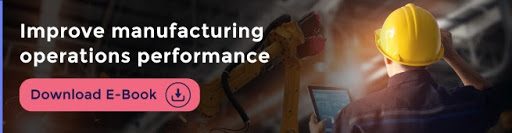
What are the 3 Types of Capacity Planning in Manufacturing?
The three primary types of capacity planning are strategic, tactical, and operational.
Each type serves a different purpose and time horizon, providing a comprehensive approach to managing production capacity. Companies can achieve a balanced approach to capacity management when these three types of planning are properly integrated.
Here’s a detailed breakdown of the three mentioned types of capacity planning:
Strategic Capacity Planning
Strategic capacity planning involves long-term planning, typically spanning several years.
This type of planning focuses on ensuring the organization has the necessary resources to meet future demands. It involves significant decisions about new facilities, equipment, and technology investments.
Strategic capacity planning is crucial for aligning the company’s long-term goals with its production capabilities.
It helps anticipate market trends, technological advancements, and changes in customer preferences, allowing the organization to stay competitive and responsive to future challenges.
Key activities in strategic capacity planning include:
- Forecasting long-term demand trends
- Evaluating potential investments in new production facilities or equipment
- Assessing the impact of technological advancements on production processes
- Developing capacity planning strategies for expansion or contraction based on market conditions
Tactical Capacity Planning
Tactical capacity planning focuses on medium-term planning, typically covering one to three years. This type of planning aims to adjust resources based on demand fluctuations and seasonal variations.
Tactical capacity planning involves optimizing existing resources to meet anticipated demand without significant long-term investments.
It includes workforce planning, scheduling maintenance, and managing inventory levels.
Key activities in tactical capacity planning include:
- Analyzing historical demand patterns and seasonal trends
- Adjusting workforce levels through hiring, training, or temporary staffing
- Scheduling preventive maintenance to minimize downtime
- Managing inventory levels to ensure sufficient stock without overproduction
Operational Capacity Planning
Operational capacity planning is concerned with short-term planning, usually covering daily, weekly, or monthly time frames. This type of planning focuses on optimizing resource utilization to meet immediate production requirements.
Operational capacity planning involves detailed scheduling of production activities, workforce assignments, and equipment usage. It ensures that the organization can respond quickly to changes in demand and maintain efficient production processes.
Key activities in operational capacity planning include:
- Creating detailed production schedules based on current orders
- Assigning workforce tasks and shifts to meet production targets
- Monitoring equipment performance and addressing any issues promptly
- Coordinating with suppliers to ensure timely delivery of raw materials
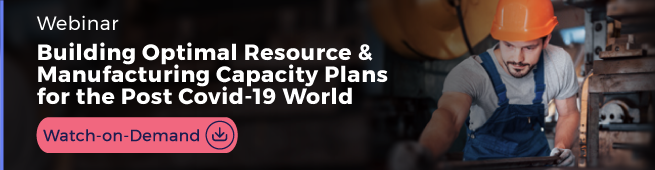
What is Resource Planning?
Resource planning is a capacity planning component that carefully analyzes available resources to determine the optimal production schedule and capacity requirements.
Resource planning ensures an organization has the necessary resources to meet future demands effectively.
It enables manufacturers to:
- Identify potential resource constraints and bottlenecks in the production process
- Allocate resources effectively to meet production targets and customer demands
- Optimize the utilization of resources, reducing idle time and maximizing productivity
- Anticipate future resource needs and proactively acquire or allocate them
- Ensure that the right resources are available at the right time to maintain production schedules
Effective resource planning requires a deep understanding of the manufacturing process, available resources’ capabilities, and resource constraints’ potential impact on production output.
Organizations can model different resource allocation scenarios and optimize their resource plans accordingly using data analytics and simulation tools.
What are Manufacturing Capacity Planning Variables?
Manufacturing capacity planning variables are production volume, labor availability, equipment availability, material availability, and facility constraints.
Each of these factors plays a significant role in determining the overall capacity of a manufacturing operation.
Below, we’ll go over each variable in detail:
Production Volume
Production volume is the most fundamental variable in capacity planning. It refers to the quantity of products a manufacturing facility can produce within a given time frame.
Accurate forecasting of production volume is essential to ensure the facility can meet customer demands without overproducing or underproducing.
This involves analyzing historical sales data, market trends, and customer orders to predict future demand accurately.
Labor Availability
Labor availability aims to ensure enough skilled workers are available to meet production requirements.
Labor shortages can lead to production delays and decreased output, while excess labor can increase operational costs.
Effective labor management includes workforce planning, training programs, and flexible staffing arrangements to adapt to changing production needs.
Equipment Availability
Equipment availability refers to the readiness and reliability of machinery and equipment used in production. Regular maintenance, timely repairs, and equipment upgrades are necessary to prevent breakdowns and ensure continuous production.
Capacity planning must monitor equipment downtime and schedule preventive maintenance to minimize disruptions.
Material Availability
Material availability involves ensuring that the necessary raw materials and components are available when needed. Supply chain disruptions, material delivery delays, and material price fluctuations can impact production schedules.
Effective material management includes maintaining optimal inventory levels, establishing reliable supplier relationships, and implementing just-in-time (JIT) inventory practices to reduce material shortages and excesses.
Facility Constraints
Facility constraints refer to the physical limitations of the manufacturing facility, such as space, layout, and infrastructure.
These constraints can impact the flow of materials, equipment placement, and the production process’s overall efficiency.
Capacity planning must consider these constraints and optimize the facility layout to maximize space utilization and streamline production workflows.
Additional Variables
In addition to the primary variables mentioned above, several other factors can influence manufacturing capacity planning:
- Lead Times is the time required to procure materials, produce goods, and deliver finished products to customers.
- Quality Control ensures that products meet quality standards and reduces the rate of defects and rework.
- Regulatory Compliance adheres to industry regulations and standards that may impact production processes and capacity.
- Integrating advanced technologies such as automation, artificial intelligence-powered capacity planning, and data analytics enhances production efficiency and capacity.
What are Capacity Planning Challenges?
The challenges of capacity planning are inaccurate forecasting, demand volatility, supply chain disruptions, resource constraints, difficulties with technological integration, and regulatory compliance.
These challenges often complicate this process, making it difficult for organizations to utilize optimal capacity.
Here is a short list of common challenges faced in capacity planning:
Inaccurate Forecasting
Forecasting errors can lead to either overestimating or underestimating the required capacity.
Overestimating demand can result in excess inventory and increased holding costs. In contrast, underestimating demand can lead to stockouts, missed sales opportunities, and dissatisfied customers.
Factors such as market volatility, changing customer preferences, and introducing new products can all contribute to forecasting inaccuracies.
Demand Volatility
Demand volatility refers to the fluctuations in customer demand that can occur due to various factors such as seasonal changes, economic conditions, and competitive actions.
High demand volatility makes it challenging to plan capacity accurately, as it requires organizations to be flexible and responsive to sudden changes in demand. This volatility can lead to inefficiencies in production scheduling and resource allocation, ultimately affecting the overall performance of the manufacturing operations.
Supply Chain Disruptions
Supply chain disruptions, such as delays in raw material deliveries, transportation issues, and supplier failures, can significantly impact capacity planning.
These disruptions can cause production delays, increase lead times, and reduce the overall efficiency of the manufacturing process.
Mitigating the impact of supply chain disruptions requires organizations to develop comprehensive contingency plans and maintain strong relationships with multiple suppliers to ensure a steady flow of materials.
Resource Constraints
Resource constraints, including labor, equipment, and facilities limitations, can hinder effective capacity planning.
For instance, a shortage of skilled labor can lead to production bottlenecks. At the same time, outdated or insufficient equipment can reduce production efficiency.
Additionally, physical constraints within the manufacturing facility, such as limited space or inadequate infrastructure, can restrict the ability to scale up production.
Addressing these constraints requires strategic investments in workforce development, equipment upgrades, and facility expansion.
Technological Integration
It can be challenging to integrate advanced technologies such as automation, artificial intelligence, and data analytics into the capacity planning process.
While these technologies offer significant benefits in improved accuracy and efficiency, their implementation requires substantial investments in infrastructure, training, and change management.
Organizations must carefully plan and manage the integration of these technologies to ensure a smooth transition and maximize their potential benefits.
Regulatory Compliance
Manufacturing operations are often subject to various regulatory requirements related to safety, quality, and environmental standards.
Ensuring Compliance with these regulations can add complexity to the capacity planning process. Non-compliance can result in legal penalties, production shutdowns, and damage to the organization’s reputation.
Therefore, capacity planning must incorporate regulatory considerations to ensure that all operations adhere to the required standards.
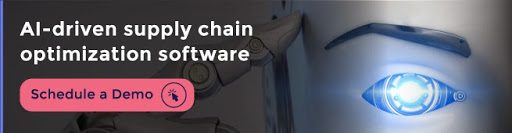
What are the Best Practices for Manufacturing Capacity Planning?
Best practices for manufacturing capacity planning are regularly reviewing and updating the plan, developing and involving cross-functional teams, utilizing advanced analytics, implementing lean manufacturing principles, maintaining flexibility and agility, and continuously monitoring and improving the process.
Regularly Review and Update the Capacity Planning Plan
One of the most critical best practices is regularly reviewing and updating the capacity planning plan. This ensures the plan aligns with current market conditions, production capabilities, and customer demands.
Regular updates help identify potential bottlenecks and make necessary adjustments to avoid disruptions.
Involve Cross-Functional Teams in the Planning Process
Involving cross-functional teams in capacity planning is crucial for gaining diverse perspectives and insights.
Teams from production, sales, marketing, finance, and supply chain should collaborate to ensure that all aspects of the business are considered. This collaborative approach helps in creating a more comprehensive and realistic capacity plan.
Utilize Advanced Analytics and Forecasting Tools
Leveraging advanced analytics and forecasting tools can significantly enhance the accuracy of capacity planning. These tools use historical data, market trends, and predictive analytics to provide more accurate demand forecasts.
Integrating these insights into the capacity planning process helps companies make more informed decisions and optimize resource allocation.
Implement Lean Manufacturing Principles
Implementing lean manufacturing principles can help reduce waste, improve efficiency, and increase production capacity.
Lean principles focus on streamlining processes, eliminating non-value-added activities, and continuously improving operations. Companies must adopt lean practices to enhance their capacity planning efforts and achieve better operational performance.
Maintain Flexibility and Agility in the Production Process
Maintaining flexibility and agility in the production process is essential for responding to demand and market conditions changes.
Flexible manufacturing systems, modular production lines, and adaptable workforce arrangements can help companies quickly scale up or down based on demand fluctuations.
This agility ensures the company can meet customer needs without compromising efficiency or quality.
Continuous Monitoring and Improvement
Continuous monitoring and improvement of the capacity planning process are vital for long-term success.
Regularly tracking key performance indicators (KPIs) such as production efficiency, equipment utilization, and order fulfillment rates helps identify areas for improvement.
Implementing a culture of continuous improvement ensures that the capacity planning process evolves and adapts to changing business needs.
What’s the Role of Technology in Capacity Planning?
The role of technology in manufacturing capacity planning is to provide real-time data, optimize production schedules, and enhance decision-making processes.
ERP systems, MES, and APS software enable organizations to plan their capacity more effectively, respond swiftly to market demands, and achieve higher operational efficiency.
Here are some key technologies that significantly impact capacity planning:
Enterprise Resource Planning (ERP) Systems
Enterprise Resource Planning (ERP) systems are comprehensive software platforms integrating various business processes, including finance, human resources, procurement, and manufacturing.
In the context of manufacturing capacity planning, ERP systems provide a centralized database that offers real-time visibility into production schedules, inventory levels, and resource availability.
This integration allows for more accurate forecasting, better coordination across departments, and streamlined decision-making processes.Key benefits of ERP systems in capacity planning include:
- Real-time Data Access
ERP systems provide up-to-date information on production status, inventory levels, and resource utilization, enabling more accurate capacity planning. - Improved Coordination
ERP systems facilitate better communication and coordination across departments, reducing the risk of bottlenecks and inefficiencies. - Enhanced Forecasting
ERP systems use historical data and advanced analytics to improve demand forecasting, helping organizations plan their capacity more effectively.
Manufacturing Execution Systems (MES)
Manufacturing Execution Systems (MES) are specialized software solutions designed to monitor and control manufacturing operations on the shop floor. MES systems collect real-time data from production equipment, track work-in-progress, and provide insights into production performance.
This information is crucial for capacity planning, as it helps organizations identify potential bottlenecks, optimize production schedules, and ensure that resources are used efficiently.
Key benefits of MES systems in capacity planning include:
- Real-time Monitoring
MES systems provide real-time visibility into production processes, allowing organizations to quickly identify and address issues that could impact capacity. - Improved Efficiency
MES systems help organizations optimize their production schedules and reduce downtime since they track work-in-progress and equipment performance. - Enhanced Quality Control
MES systems monitor production quality in real time, enabling organizations to identify and address quality issues before they impact capacity.
Advanced Planning and Scheduling (APS) Software
Advanced Planning and Scheduling (APS) software optimizes production planning and scheduling by considering various constraints, such as resource availability, production capacity, and demand forecasts.
APS systems use sophisticated algorithms and data analytics to generate optimal production schedules that maximize resource utilization and minimize production costs.
Key benefits of APS software in capacity planning include:
- Optimized Scheduling
APS software generates production schedules considering various constraints and optimizing resource utilization, helping organizations meet demand more efficiently.
- Improved Flexibility
APS systems enable organizations to quickly adjust their production schedules in response to demand or resource availability changes, enhancing their ability to respond to market fluctuations.
- Enhanced Decision-Making
APS software provides detailed insights into production performance and resource utilization, enabling organizations to make more informed capacity planning decisions.
How ThroughPut Software Helps Manufacturers with Capacity Planning
ThroughPut’s capacity planning software utilizes AI to streamline capacity planning for manufacturers, optimizing resource allocation and operational performance.
It generates accurate demand forecasts, minimizing overproduction and underproduction risks, leading to better inventory management and cost savings.
The software automates resource adjustments in real-time, allowing for swift adaptation to demand changes, minimizing downtime, and maximizing productivity.
ThroughPut also offers real-time monitoring, analytics, and predictive maintenance to improve production efficiency and equipment reliability.
Its scalability, flexibility, and seamless integration with existing systems help manufacturers optimize processes, reduce costs, and drive profitability.
Book a free demo today to boost your manufacturing capacity planning.