5 Effective Tactics to Manage Bottlenecks in Manufacturing
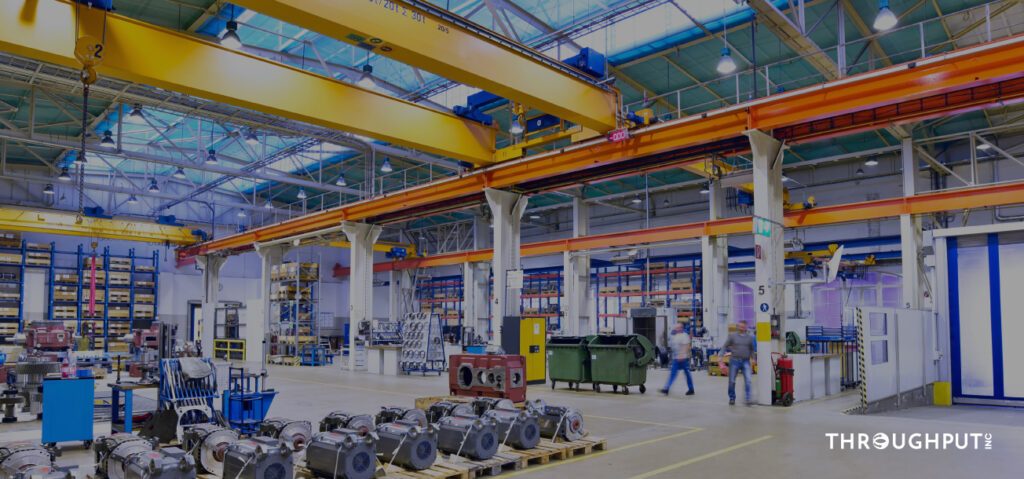
No matter how well things run, seamless operations in manufacturing is a distant dream for many. Common challenges like equipment failures and labor shortages not only disrupt production but also significantly impact output.
These challenges or what we call “bottlenecks” in manufacturing, acting as critical pinch points in production, can introduce inefficiencies and inflate operational costs, leading to delays and reduced customer satisfaction. Identifying and resolving these issues is vital for plant managers to boost throughput, optimize resources, and strengthen supply chain resilience.
In this blog, we’ll introduce you to five ways in which you can manage bottlenecks in manufacturing as a plant manager.
How to Effectively Manage Bottlenecks in Manufacturing?
Manufacturing bottlenecks fall into two categories: short-term and long-term. Short-term bottlenecks are temporary, often arising from situations like employees on vacation or unexpected sick leaves. Long-term bottlenecks, however, are ingrained in your production process and can include issues like outdated or inefficient machinery, limited production capacity, or chronic understaffing.
Either way, addressing the different types of bottlenecks requires tailored strategies to ensure smooth and efficient operations.
Here are five such effective strategies to manage bottlenecks in manufacturing.
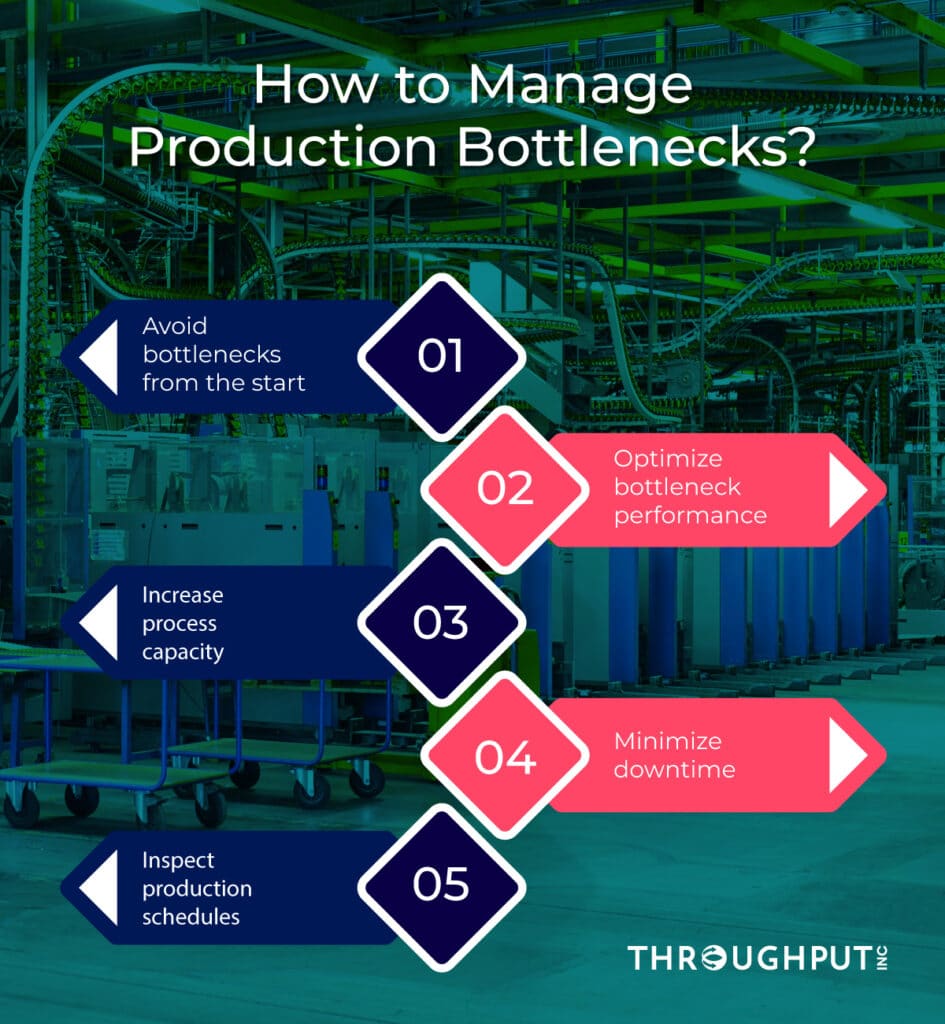
Tactic #1 – Avoid bottlenecks in manufacturing from the start
When it comes to managing bottlenecks in manufacturing, the most effective strategy is to preemptively address them. This involves identifying and eliminating any non-essential processes that may disrupt your production flow.
By consistently focusing on enhancing the efficiency of your manufacturing processes, you can take a proactive stance against potential disruptions.
Have you considered using value stream maps? They serve as an insightful tool, providing a comprehensive overview of your production line and pinpointing areas prone to inefficiency. Utilizing these types of tools enable you not only to manage existing bottlenecks in your manufacturing process but also to implement measures that prevent future ones.
This approach underscores the importance of continuous improvement and efficiency in maintaining a streamlined and effective manufacturing operation.
Tactic #2 – Optimize bottleneck performance
Managing bottlenecks in your manufacturing process is also really about getting the best performance out of the bottleneck resource itself. You want to shield this key part of your production line from any issues that might pop up from other areas, both upstream and downstream.
Ensuring that this critical part of your production line is insulated from issues in other areas is key.
Optimizing bottleneck scheduling is another crucial part. You’re looking to arrange the tasks and workflows in a way that keeps things moving smoothly, without any unnecessary hold-ups.
By doing this, you’re not just fixing immediate problems; you’re also setting up a more efficient, hassle-free process for the future.
Tactic #3 – Increase process capacity
Increasing the capacity of your overall process hinges on enhancing the capacity of the bottleneck. It’s a key focus area for plant managers.
When you improve any bottleneck resource, it’s possible that the bottleneck might shift to a different resource within the manufacturing process. This is a common occurrence in dynamic production environments.
Therefore, it’s crucial that you, as a plant manager, continually monitor the effects of any process changes. Regular observation and analysis will help you identify when and if the bottleneck changes location. This proactive approach ensures that you can swiftly respond and adjust your strategies, maintaining the efficiency and productivity of your operations.
It’s about striking a balance between improvement and adaptability in your process management.
Tactic #4 – Minimize downtime
If you’re managing a production line and your bottleneck equipment hits a snag or breaks down during operations, it’s crucial to jump into action quickly. Getting that bottleneck back up and running is your top priority.
This often means having replacement parts readily available so you don’t lose precious time waiting for them. Plus, regular preventive maintenance on your equipment can be a real game-changer; it helps avoid these breakdowns in the first place.
As a plant manager, another key area you should focus on is reducing the changeover times when switching from one product to another. These transition periods can really eat into your actual production time.
Think of it as streamlining your process to make every second count. When you minimize this downtime, you’re not just fixing immediate issues but also boosting your overall efficiency. It’s all about being prepared and making smart, timely decisions to keep things moving smoothly.
Tactic #5 – Inspect production schedules
If you’re overseeing a process that churns out various products, each taking up different amounts of time at the bottleneck, then it’s time to put on your analyst hat. By diving into your production schedule, you can work out a product mix that cleverly minimizes the overall demand on that bottleneck.
Imagine it’s like juggling different tasks; some take longer than others. Your goal is to find the right balance, where you’re not overloading the most critical part of your process. This means scheduling the production of different items in a way that keeps the bottleneck from becoming overwhelmed.
Things to Remember About Managing Bottlenecks in Manufacturing
- Effectively managing bottlenecks in manufacturing can have a significant impact on supply chain efficiency and profitability alike
- It is important to address these bottlenecks in the manufacturing process in the initial stages to avoid bigger issues
- Value stream maps are an important tool for identifying and addressing bottlenecks
- Being proactive in managing bottlenecks is the key to detecting unwanted bottlenecks
- Increasing process capacity aids in eliminating bottlenecks in your manufacturing process
- Minimizing downtime assists in improving bottleneck performance
A Final Note for Plant Managers on Manufacturing Bottlenecks
Tackling bottlenecks effectively in your manufacturing process is a crucial skill for plant managers. This blog has provided insights and strategies that, when implemented, can significantly improve your production efficiency.
Remember, identifying and actively managing bottlenecks not only prevents disruptions but also opens doors to increased productivity and cost reductions.
As a project manager, mastering bottleneck management can elevate your contribution to your organization’s supply chain success. It’s about taking the knowledge gained here to the next level.
We encourage you to deepen your understanding by downloading our whitepaper, which offers a more comprehensive exploration of bottleneck management techniques.
Your dedication to proactive bottleneck management is a vital step towards maximizing the efficiency and effectiveness of your production processes. Embrace these strategies, and you’ll be well on your way to becoming a bottleneck management expert, steering your organization towards greater operational success.