Inventory Distortion Will Cost Retailers $1.77 Trillion in 2023. Here’s How Blue Yonder Can Help.
It’s always been challenging for retailers to put the right product in the right location at the right time. But the past several years have made it seem nearly impossible, thanks to fast-changing consumer needs, increased competition, the growth of omni-channel, supply shortages, and transportation issues.
What’s the real cost of inaccurate inventory management? IHL Services, a global research and advisory firm, estimates that inventory distortion — the combined cost of lost sales from out-of-stocks, along with the deep discounts required to sell overstocks — will drive a $1.77 trillion loss for the world’s retailers in 2023 alone. That number is the equivalent of the annual revenues of the Top 10 retailers worldwide.
Blue Yonder recently co-sponsored a research study with IHL aimed at understanding the problem of inventory distortion and outlining some strategies for addressing it. Watch the “Inventory Distortion: The Good, the Bad, the Ugly” webinar, which provides an overview of the study results — or read IHL’s in-depth research report.
Here’s a quick look at what the study revealed about inventory distortion, and how Blue Yonder is helping its retail customers minimize their own losses.
The Huge Global Impact of Out-of-Stocks and Overstocks
When a customer visits a store or website and is unable to purchase the product they’re looking for, that’s more than an inconvenience. It’s a lost sale that contributes to the $1.77 trillion problem of inventory distortion. When a retailer marks down merchandise and moves it to the clearance rack, that lost margin is also a contributor.
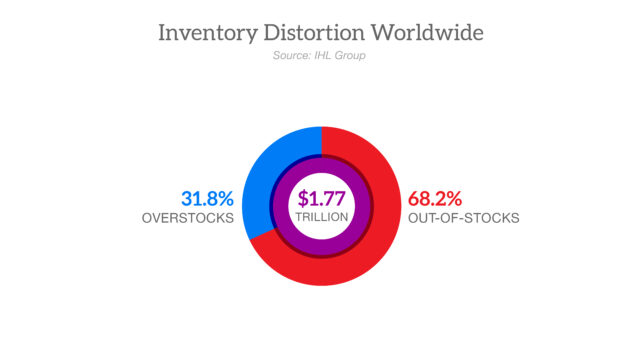
In 2023, IHL estimates that out-of-stocks will account for a $1.2 trillion loss, with overstocks contributing $562 billion in losses.
Worldwide, retailers’ overstocks performance is improving; 2023 losses were 21.6% lower than in 2022 (reductions are good). IHL attributes this improvement to more accurate inventory management, as retailers move away from “buffer” inventory policies and rely more on advanced inventory forecasting and management solutions.
But out-of-stocks remain an enormous issue. Retailers around the world only realized a 0.3% average improvement over their 2022 results in this area. In North America, retail loss due to out-of-stocks actually increased by a staggering 17.7% in 2023. While increasing retail theft in the U.S. is a contributing factor, inaccurate inventory management processes and systems remain a big driver of the out-of-stock problem globally.
How Can You Minimize Your Losses? Advanced Solutions From Blue Yonder
The first step in minimizing inventory distortion, according to IHL, is to invest in technology solutions that provide accurate, real-time inventory visibility. Today’s retail supply chains span thousands of miles, involve dozens of partners and serve multiple channels. Mastering the problem of inventory distortion begins by seeing inventory wherever it exists in this network — whether it’s an in-transit shipment from a supplier, pallets in a regional warehouse, boxes moving to stores on a truck, or individual products on the retail shelf.
Built on a foundation of APIs and advanced data-streaming technology, Blue Yonder’s Order Management (OMS) microservices are designed to deliver this real-time, enterprise-wide view of inventory across all sources, including warehouses, stores, drop-ship suppliers, and fulfillment centers.
Within the OMS suite, Blue Yonder’s Inventory microservice supports full end-to-end visibility and tracking of both sellable and non-sellable inventory. The Inventory microservice provides real-time availability at the enterprise and location level, factoring in physical proximity to the customer, to provide a realistic net available-to-promise date. Retailers can layer their own eligibility rules, safety-stock policies, selling channel configurations, supply and inventory segmentation strategies, and future supply plans on top of this data. Built using a highly scalable and performant infrastructure, Blue Yonder’s Inventory solution supports the high transaction needs of real-time, multi-location retail inventory management.
Based on this accurate, in-depth view of inventory across the network, retailers can leverage Blue Yonder’s Commits solution to identify the optimal way to allocate merchandise and fulfill customer orders, considering customer and product locations, inventory levels, merchandise costs, the likelihood of markdowns, shipping time and costs, operation costs, staffing availability, and many other criteria. Blue Yonder provides both pre- and post-order optimization in a single engine, supported by machine learning (ML), to truly optimize fulfillment from the earliest stage. Shoppers get accurate fulfillment dates before and after check-out — and retailers can reduce the cost-to-serve through sourcing optimization, while still meeting customer expectations.
Together, Blue Yonder’s Inventory and Commits solutions simplify and automate the complex process of strategically matching every consumer order, across every channel, with the right product and the right delivery service — to directly address the problem of inventory distortion. These solutions are designed to reduce both overstocks and out-of-stocks, maximizing cost and service outcomes.
Start Attacking the Problem of Inventory Distortion Today
While inventory distortion might seem an overwhelming challenge, Blue Yonder’s Order Management solutions make it easy to start minimizing your losses. This flexible suite is a set of microservices, built as individually packaged business solutions that can be deployed one at a time.
Blue Yonder is continuously releasing additional microservices and is expanding the traditional definition of order management to include capabilities from planning and forecasting to omnichannel fulfillment. Many Blue Yonder customers begin with the Inventory and Commits solutions and expand their capabilities over time, including the addition of ML and AI to power up the results. On average, our customers have three packaged microservice solutions or more — and continue to grow their solution footprint due to its value and ease of deployment.
Some of the world’s top retailers are already leveraging Blue Yonder’s Order Management microservices to reduce out-of-stocks and overstocks, significantly decreasing inventory distortion in their supply chains. Explore the benefits for your business by contacting us today – to schedule a discovery call and get a demo booked.
You can also learn more about “The Good The Bad and The Ugly of Inventory Distortion” by downloading the report and watching the webinar.