The main goal of the supply chain optimization model is to meet customer demand while minimizing costs and maximizing profits, taking into account all limitations. It uses advanced analytics to balance supply and demand, ensuring that enough raw materials are acquired for manufacturing and distribution in the most cost-effective way to meet customer expectations. While working with various optimization models, I often encountered situations where the model would make decisions to produce items even when there was no demand, resulting in holding inventory. Based on my observations, I have identified scenarios that led to the optimization models producing and storing excess inventory.
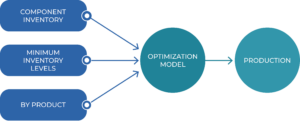
Fig 1.1: Supply Chain Optimization
Scenario 1: Component Inventory holding cost
Inventory holding cost refers to the expenses incurred by a business to store inventory. It is a crucial factor in decision-making for optimization models. These costs can be associated with holding finished goods inventory or the components used in producing finished goods. In Figures 1.2 and 1.3 below, we can observe that producing “FG item 1” requires the consumption of 5 components. The figures show the quantity of component usage, the current inventory status of each component, and the associated inventory holding cost. The total inventory holding cost for all 5 components is $9.5. When we consider the finished product, the production cost for “FG item 1” is $3, and the inventory holding cost for the finished goods is $4. Hence, the total cost of producing and holding “FG item 1” is $7. Since the cost of producing and storing a finished goods item is lower than the holding cost of the components, optimization models are driven to produce and hold the finished goods inventory, even when there is no demand for the goods.
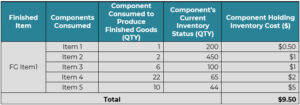
Fig 1.2: Calculation of Component Holding Inventory Cost

Fig 1.3: Calculation of Finished Goods Cost
Scenario 2: Minimum Inventory Levels
Minimum inventory levels refer to the lowest quantity of inventory required for each SKU (stock-keeping unit) to fulfill customer demand. In certain situations, the planner may anticipate future demand and establish a minimum inventory level for a particular SKU. This constraint then influences the optimization model to produce the finished goods item to meet the minimum inventory requirements.
Scenario 3: By Product
A By-Product is created during the manufacturing process that creates multiple products. It is produced during the production process of the main product. It is the ‘by default’ result of the production process.
For example, Ethylene- a by-product of petroleum refinery – is an essential ingredient used in manufacturing polystyrene, polyvinyl chloride (PVC), and polyethylene-based products i.e. Plastic products. A high penalty for not meeting the demand for a by-product could result in the production of a by-product along with the main product where we don’t see any demand relate to it.
Conclusion
Optimization models exhibit certain behaviors, such as the accumulation of inventory without demand, which can be influenced by specific parameters and constraints. To avoid these issues, planners can employ penalty functions or relax certain constraints to tackle these challenges effectively. Arkieva’s supply planning tool offers the necessary flexibility and capability to handle these optimization challenges within the supply chain.