Navigating the Red Sea Crisis with Blue Yonder’s Control Tower Insights
Since mid-November, Houthi rebels in Yemen have intensified their assaults on commercial shipping vessels navigating through the lower Red Sea, in response to the situation in Gaza. Reacting to the situation, ocean cargo rates have surged. By one estimate, “Ocean freight rates have increased by more than 200% since the Red Sea crisis escalated in mid-December.”
The Red Sea facilitates around 12% of worldwide trade, which includes approximately 30% of global container traffic. Every year traded goods and supplies worth billions of dollars transit through the Red Sea. While the impact of the current crisis is wide, the main types of goods impacted are oil, corn, tea, electronics, raw goods, and finished-to-quick retail fashion. Some analysts predict that repercussions on oil transported from this region may have long-term consequences.
Certain vessels are being redirected around the Cape of Good Hope, situated at the southernmost point of Africa, which is causing an increase in their travel duration of up to two weeks. Currently, the average delay for shipping vessels around the Cape of Good Hope is 9–12 days versus the direct route. Given the current circumstances, some ocean cargo liners are relying on local intel in the region to determine the safety of the waterway and some prominent shipping companies have chosen not to utilize the Red Sea for transport.
The net impact is slowing down the inventory and availability of finished goods, as well as raw materials to complete the goods. We may see more with regards to “shrinkflation” (i.e., keep the price the same, but reduce packaging and size as a response). We initially predict EMEA markets will be impacted immediately by this unrest and see extended impact in NA/SA regions.
Navigating the Red Sea Crisis: Using Blue Yonder Visibility and Predictive Analytics
Given the circumstances, Blue Yonder is well-equipped to support our customers through the application of visibility and predictive analytics, utilizing solutions like Control Tower. We can assess through the application of various points of interest, to provide strategic options during times of conflict such as this.
Critical congestion, cost, and inventory impact, to name a few, can be determined via Control Tower’s advanced analytics and Chokepoint Report. In addition, the Control Tower dashboard can help collectively navigate the customer’s supply chain through this unrest.
Right now, Blue Yonder’s Control Tower solution is helping customers track their re-routed shipments from the Red Sea through the Cape of Good Hope, addressing errors, inventory, and original and predicted arrival dates to mitigate surprises for our customers’ clients or end-line consumers.
Customers can see the original ETA and the new Predicted Time of Arrival (PTA) to see how their downstream supply will be affected primarily in two ways.
The first way is the use of Advanced Searches in the Dashboard Map and Shipment Detail screens that show how a shipment originating in Europe, and usually routed through the Mediterranean Sea and the Red Sea, is getting re-routed through South Africa’s Cape Hope to get to a port at the end of the Red Sea.
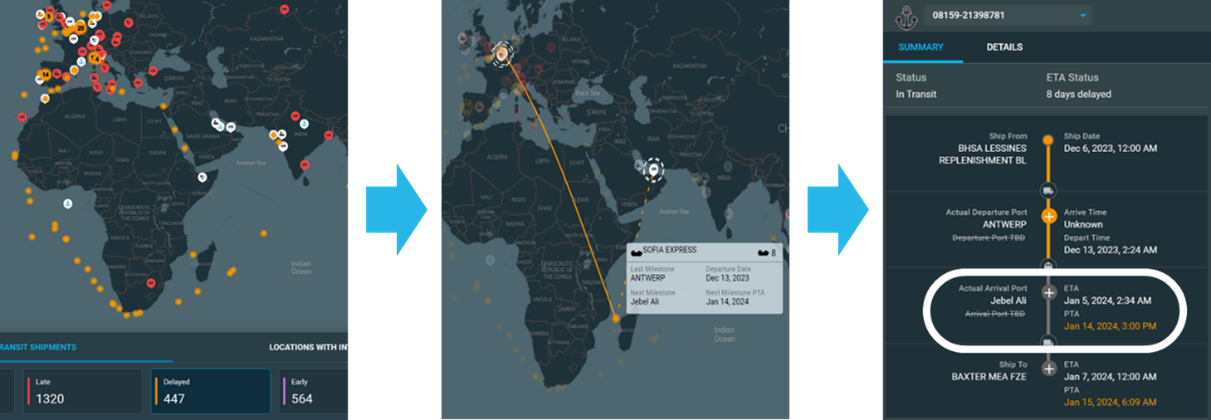
When a ship approaches the conflict zone in the Red Sea, customers can utilize the Chokepoint Report. This report offers visibility and status updates on shipments near major chokepoints, which are natural congestion points along crucial passages. In the Red Sea, the primary chokepoints are Bab-ell-Mandeb and the Suez Canal. Control Tower’s Chokepoint Report also aids in analyzing route bearings to ascertain a ship’s direction and consider other vessels heading towards these chokepoints.
Secondly, we can address the error rate in the approach with geofence and geo-pings to determine when a ship passed the chokepoint.
Options within the Control Tower report validate critical data to help customers make better decisions when it comes to their shipments and inventory.
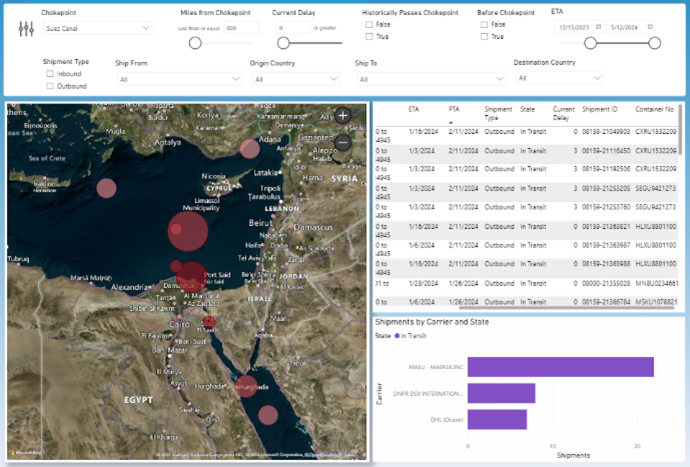
In conclusion, as the crisis in the Red Sea unfolds, the impact on global trade and shipping operations is substantial. Blue Yonder recognizes the urgency and complexity of the situation and is committed to providing strategic support through our advanced solutions. Control Tower’s sophisticated analytics and Chokepoint Report help our customers navigate critical congestion, assess costs, and manage inventory impact efficiently. With the ongoing rerouting of shipments through the Cape of Good Hope, our Control Tower dashboard enables customers to track, address errors, and anticipate arrival dates, and help minimize disruptions in the supply chain.
As we monitor the evolving situation, Blue Yonder remains dedicated to empowering our customers with timely and informed decision-making tools to mitigate challenges and navigate through this period of unrest.