Warehouse Management Systems are the Heartbeat of Distribution Centers
I recently did some work exploring the world of Warehouse Management Systems – which a professional in the 3PL field called “the heartbeat of a DC- you can’t run one without it!”. My interest in this area led me to conduct some benchmarking research from professionals who are experienced in the acquisition and implementation of warehouse management systems. What follows are a few insights.
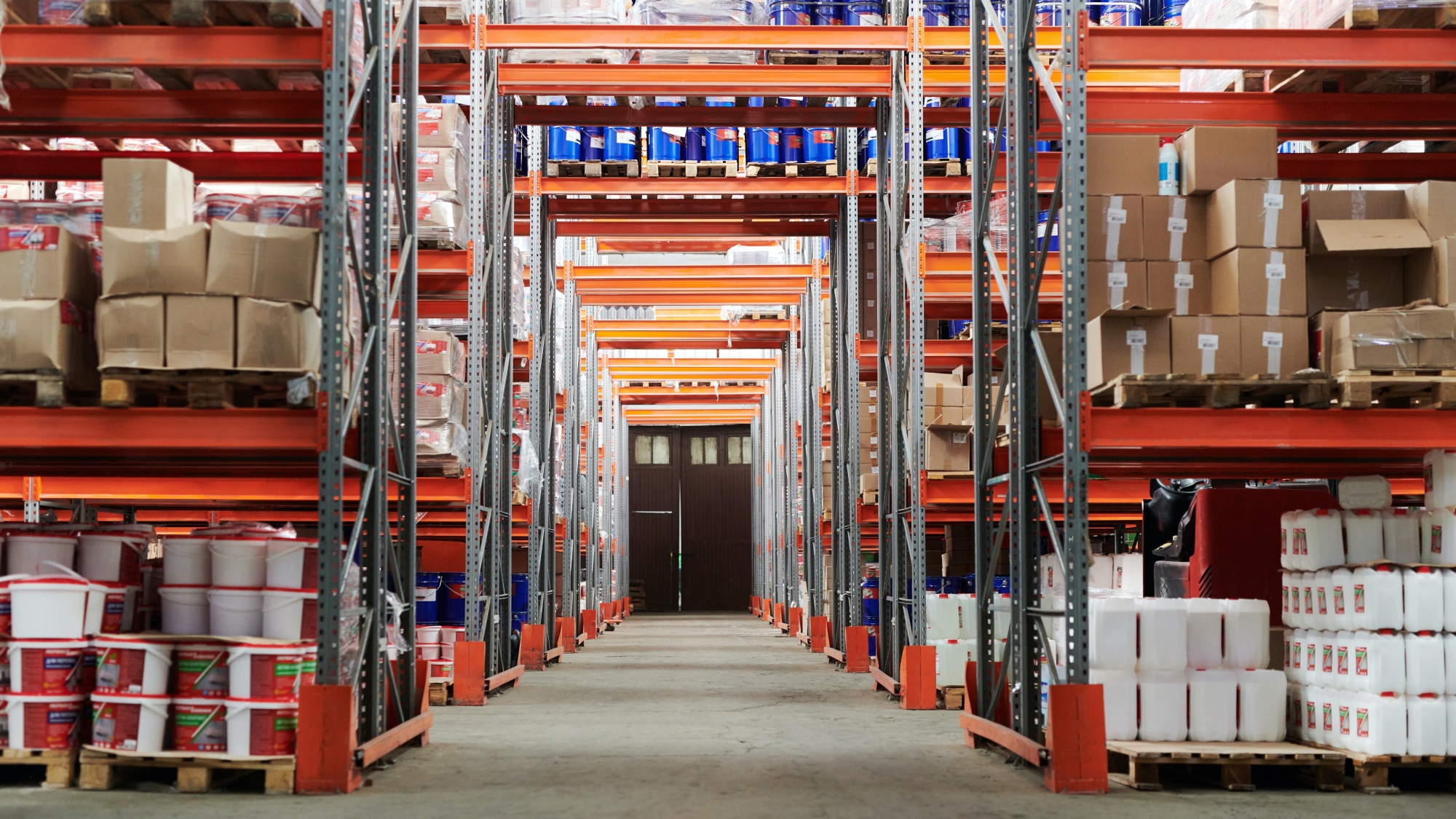
There are a number of different types of warehouse management systems (WMS) that have different features, different levels of configuration, and are often described in terms of “tiers”. Tier 1 WMS’s are generally considered the most sophisticated (Manhattan Associates, Red Prairie, etc) , whereas tier 2 and tier 3 WMS’s (High Jump, Catalyst, EXE, McHugh, Zethcon, and others may be less sophisticated.
The Gartner report on WMS’s describes a warehouse management system (WMS) as “a software application that helps manage and intelligently execute the operations of a warehouse or distribution center (DC).” WMS applications offer capabilities such as:
- Receiving
- Put-away
- Stock locating
- Inventory management
- Cycle counting
- Task interleaving
- Wave planning
- Order allocation
- Order picking
- Replenishment
- Packing
- Shipping
- Labor management
- Automated material handling equipment (MHE) interfaces
These systems natively exploit mobile devices along with bar code and, possibly, RFID scanning/sensing to form the transactional foundation of a WMS. This enables efficiencies of directed work activity and the delivery of accurate information in near real time. Gartner includes integrated functionality — what we refer to as extended WMS capabilities (see Apply an Architectural Framework to Stratifying Warehouse Management Systems) — as components of a WMS evaluation.
These extended WMS capabilities include:
- Workforce/labor management
- Slotting
- Yard management
- Voice picking
- Parcel manifesting
- Value-added services such as light manufacturing/kitting
- Third-party logistics (3PL) billing
I interviewed Clark Koch, a subject matter expert who has implemented a number of different WMS systems, working as a consulting partner for one of the largest and most notable WMS’s, Manhattan Associates. He was involved in deploying the MA system for a number of consumer brands and retailers, including Cabela’s, REI, Puma, and Regal Logistics. He notes that a big factor influencing the cost of the WMS implementation involves the degree of “customization” that is required, which refers to the level of modification required to meet the warehouse requirements. It is highly unusual to simply go with “no modification” – as there is always some level of customization, but the degree of customization increases costs substantially. The implementation typically involves a team of 12 to 15 people, which includes programmers/consultants, and developers, and also includes people pulled in from the client’s business to help provide input into the design of the WMS>
The stages of implementation are as follows:
- Design Stage– A project team is formed consisting of 12 to 15 people in the design sessions, often pulling people in from different divisions. The design phase is fairly lengthy, depending if there are significant modifications. This typically will take 3 or 4 months to get through the design of the system, and identify all of the features (noted above) and how they will need to be configured. This also includes how the system will interact with the ERP system used by the company.
- Development and Integration Stage – In the next phase, the programmers and developers from the implementation team work with Manhattan (or whatever software is used) to develop the application to meet the design specification. Part of that also involves working conjunction with the development team. This would also include “integration”, which refers connecting the WMS so it can interact with the ERP system that takes orders from customers and operates inventory and financial reporting. At many companies, the ERP system was an “SAP” system, and is where the WMS system obtained the orders and inventory. Integration is part of the design and development process, and involves integration of development. The development and integration phase is lengthy, and will typically involve 10 developers working for 3 – 4 months.
- Testing – once the developers and programmers are able to get the system up and running, it goes to the testing phase. At this point, developerare are “breaking in” the system, and this includes developing and running through “testing scripts” to ensure the system operates well. This may take another 2 to 3 months of testing, which is to break in the system and fix any problems that come up. Note that more modification can cause more problems that need to be fixed in testing.
- Training and implementation – this is a huge piece, and have to deal with change and getting people to change. This can be another 3 – 4 months. In general, the projects are 12 – 14 months from start to finish, and just includes the software development.
- Hardware is additional, and may include printers, Radio frequency handheld devices, computers, sortation, conveyors, etc. The simplest in Manhattan is to create a “pick wave” – where the pick list is downloaded to users on a handheld device, and they are directed to go to each location. They scan a representative case – and if there is more than one, they pick that amount. The system optimizes pick paths to improve flow, and this ensures productivity is improved. It is also “dummy proof” and ensures workers cannot be allowed to make mistakes. Barcodes are already included on every package, and these would be programmed into the system.
As robotic technology continues to mature, more and more of these tasks may become automated. But the WMS will still function as the heartbeat of the system!