Industrial equipment manufacturers today are operating in an increasingly complex and ever-evolving landscape. Pressures to address and adhere to global climate control measures and the demand for more personalized products are pushing companies. In this sector. they need to to swiftly transform their operations. Furthermore, the manufacturing workforce gap is a growing concern across all industries. It is necessitating improved visibility, efficiency and control of manufacturing production and operations. This is done within and across global and local plants.
Competition is intensifying with industrial equipment companies racing to out-innovate each other. Agility and the ability to adapt to today’s complex industry trends become key to successful and competitive production and operations.
Trends and Business Drivers Shaping Industrial Equipment
The following represent key trends and opportunity drivers that industrial equipment manufacturers should address in order to be in the best position to capture the greatest market share:
- Production of one: Rising customer demand for customized products require manufacturers to be more flexible and agile.
- Self-aware software driven systems: Having a smarter, more connected system supports autonomous equipment to improve production performance.
- Enterprise agility: Agile enterprises can respond quickly and effectively to changes in market demand and increase the speed of delivery.
- Product as a service: Product as a service offers more effective business operations and a simpler financial model based on pay-per-use or pay-per-outcome.
- Enterprise risk planning: In a highly disruptive business environment, more effective risk management has become a necessity for companies.
- Circular innovation: With the world shifting towards sustainability, companies need to meet the increased demand for sustainable equipment and products.
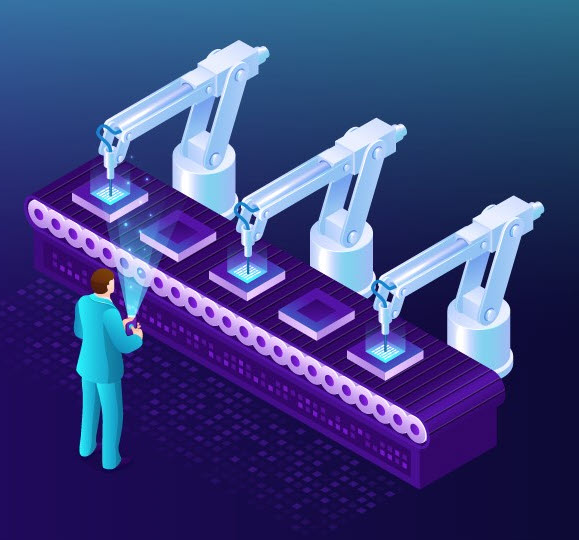
In our experience, best-in-class manufacturers are able turn these business drivers and challenges into opportunities to innovate. Leveraging the right solution, industrial equipment companies can achieve this by targeting one of the weaker links in the value chain: the gap between production and warehouse management.
How DELMIA Software Helps Industrial Equipment Companies
With DELMIA’s integrated solution, industrial equipment manufacturers can bridge this gap by mitigating disruptions that hinder shop floor and operational efficiency and drive seamless workflows, leveraging what we call ‘material synchronization.’
DELMIA’s solution for material synchronization enables industrial equipment companies to connect and improve inbound material flows, line-supply and outbound material flows. The synchronization of material flows tightly unifies manufacturing operations with warehouse processes. It coordinates production orders and the manufacturing bill of materials (MBOM) with inventory management inside plants and across the supply chain, which includes:
- Work In Progress (WIP)
- Raw materials
- Purchased parts from suppliers warehoused on-site or off-site
- Semi-finished inventory residing at a feeder production line or work cell
What’s more, material synchronization with DELMIA enables industrial equipment manufacturers to gain full visibility into orders, inventory, resources and quality status—all consolidated and easily accessible on the same platform. And when issues arise, the solution immediately notifies operators, providing optimal decision support and increasing responsiveness to disruptions.
Empowering Companies to Command Processes
DELMIA’s solution for material synchronization empowers companies to fully master the entire production process and improve lead time with these capabilities:
- Pull-based (demand driven) and one-piece flow production to eliminate inventory buffers and obsolescence.
- Material flow automation and pull signal and task generation from the final assembly to enable Just in Time and Sequence (JIT/JIS) manufacturing.
- Lean manufacturing to drive lean manufacturing principles across the value chain and achieve sustainable and profitable goals.
- Real-time synchronization of multiple sub-assembly and material kitting operations for accurate inventory replenishment.
- Consistent validation of all transported and received materials to ensure better traceability and quality assurance.
- Real-time error proofing for print, packaging and labeling inventory to minimize shipping and receiving errors.
In addition, leveraging DELMIA’s integrated solution to synchronize materials and logistics with the shop floor in real time helps unlock the following benefits:
- 24-45% reduction in inventory
- 25% increase in throughput/productivity
- Significant quality and safety improvements
Interested in learning more?
Discover more information on the value of material synchronization for Industrial Equipment companies and learn about the benefits that can be achieved. Download our ebook Master the Production Process with Material Synchronization today.
Watch the video: