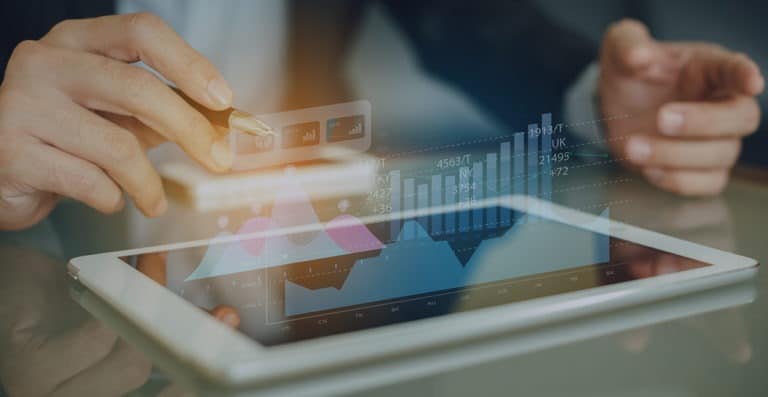
Based on thousands of discussions with Logility customers and prospects, we know many supply chain industry professionals are willing to grant that integrated business planning (IBP) and operational excellence are not synonymous. Nevertheless, you might be wondering if there’s enough of a distinction to say that IBP enables operational excellence.
Let’s start by defining operational excellence. It suffers from an identity crisis. ‘Operational’ naturally gets conflated with ‘operations’, which leads some to assume that operational excellence must be a framework and a set of tools for driving cost out of your organization. It’s ruthless cost-cutting raised to an art form, fueled by skepticism, continuous questioning and process improvement. Sometimes it happens via a major initiative that causes great upheaval in a business; other times it’s achieved via a slow, relentless grind, like glaciers reshaping the contour of the landscape.
What is Operational Excellence?
Consider two companies with identical strategies. One consistently outperforms the other, as measured by returning value to stakeholders. How? It operates better, or put another way, it executes the strategy more effectively over time.
Note that we’re not restricting operational excellence as appropriate for only certain business strategies, e.g. those centered on productivity and efficiency. Operational excellence is very much about sustained growth and bringing value to customers. Also, it’s important to note that operational excellence is cultural.
Here are some helpful insights:
Operational excellence is a mindset that embraces certain principles and tools to create sustainable improvement within an organization. Or, to put it more simply, operational excellence is achieved when every member of an organization can see the flow of value to the customer.
Ultimately, operational excellence is not just about reducing costs or increasing productivity in the workplace. It’s about creating the company culture that will allow you to produce valuable products and services for your customers and achieve long-term sustainable growth.
Operational excellence is a philosophy of the workplace where problem-solving, teamwork, and leadership results in the ongoing improvement of an organization. The process involves focusing on the customers’ needs, keeping the employees positive and empowered, and continually improving the current activities in the workplace. Operational excellence is the execution of the business strategy more effectively and consistently than the competition. This occurs when every employee can see the flow of value to the customer and fix it when the flow is interrupted.
Long-Standing Fundamentals
Operational excellence grew out of the classic “principles of excellence” and continuous improvement philosophies like Six Sigma, Lean and Shigeo Shingo’s ten guiding principles for building a resilient culture of organizational excellence:
1. Respect every individual
2. Lead with humility
3. Seek perfection
4. Assure quality at the source
5. Flow and pull value
6. Embrace scientific thinking
7. Focus on process
8. Think systemically
9. Create constancy of purpose
10. Create value for the customer
Now that we’ve covered the definition of operational excellence and its core principles, the question becomes: Does IBP align with operational excellence? If so, how?
Evidence That IBP Enables Operational Excellence
The quick take: integrated business planning is long-range strategic business planning that combines volumetric and financial data into a single, highly visual comprehensive planning platform that delivers greater global visibility, more powerful multi-scenario analysis over longer planning horizons, tighter collaborative workflow, and a wider spectrum of alerts.
From experience with thousands of customers, here’s Logility’s list of what the most effective IBP implementations have in common.
The CEO owns the process. The CEO enables acceptance and delivery of IBP at all levels in the business, and must inspire the team to view IBP not as “another project laden with department-level redundancies” but simply how the organization operates.
Sales contributes to the demand plan. Those closest to the customer have the best grasp of activity at the point of consumption, and therefore must be strongly involved and prepared to contribute to the demand plan.
Finance is at the table, not a mere observer. The finance team’s participation is critical for testing different scenarios and protecting the integrity of financial projections.
Think beyond the annual budget. IBP done correctly integrates the strategy with the business plan and ensures the delivery of both. In fact, you may find that IBP nudges your business toward a continuously updated two- or three-year financial plan.
Don’t let details derail. Too many organizations make the mistake of plunging down rabbit holes and forming committees to explore minutiae. Looking at the bigger picture frees the organization to focus on higher-level planning needed for sustaining growth and improving margins.
Get the culture right. Not surprisingly, IBP efforts often focus on process and data. However, the best deployment plans consider the cultural context and never lose sight of the following:
1. A basic requirement for effective IBP is a culture that celebrates cross-functional collaboration not as a ‘nice-to-have’ but as a requirement for executing company strategy;
2. A culture accustomed to ‘delegating upward’ will bog down the executive review portion of IBP and reduce the speed of decision-making. IBP thrives when the lowest levels of the organization are empowered;
3. IBP places a premium on data-driven decision-making. But many challenging decisions will continue to rely on judgement. The culture should value seasoned judgment and not recast it as “guesses we made before we had all the data.”
We could devote another blog post or two to thoroughly mapping the 10 operational excellence core principles to IBP best practices. But for now, let’s highlight a few clear areas of overlap that serve as evidence that IBP enables operational excellence.
Operational Excellence | IBP |
Respect Every Individual. This helps everyone feel more empowered and motivated to contribute in a positive way. | IBP thrives when the lowest levels of the organization are empowered. |
Innovation stems from experimentation and adjustments. Embrace scientific thinking. | Respect data; allow it to guide dispassionate decision-making. |
Create constancy of purpose. | IBP is simply how the organization operates. |
In summary, operational excellence is about much more than organized, repeated expense reduction. Indeed, it’s very much a growth framework laser-focused on delivering value to customers. And IBP aligns very well with the key pillars of operational excellence.
Want to learn more about how to make integrated business planning a success for your business? Read more here.
Written by
Kevin McInturff
Chief Technology Officer
Short bio
Kevin serves as the Chief Technology Officer at Logility. Before joining Logility, Kevin’s career included management positions at Deluxe Corporation, BitPay, PrimeRevenue, Global Payments, and more. He has over 20 years of experience in enterprise software leadership, including time spent in startups and large enterprises. He’s passionate about people, solving valuable market problems, and technology. Kevin has his Bachelor of Science in Computer Science from Georgia Institute of Technology and a Masters of Science Degree in Management of Technology from Georgia Tech Scheller College of Business.