Given the break-neck pace at which the markets function, supply chain executives must think on their feet to stay ahead of the competition. Each day brings possibilities and factors, turning the decision-making job into an unenviable task. Making the correct decision requires an eclectic mix of experience and knowledge, the foundation of sound judgment.
Errors in judgment come with both far-reaching and immediate consequences. That's why relying on gut instinct or experience alone or reviewing very few KPIs can sometimes spell severe impact. Now, consider technology helping you simulate the market by creating a digital twin using different distribution models. You can use this simulation to compare production to inventory statistics and make educated trade-off decisions. Supply chain optimization is a must to meet the new needs and supply chain issues. Supply chain managers must stay ahead of the curve to anticipate developments. Supply chain optimization aims to ensure that a production and distribution supply chain runs as efficiently as possible. This comprises effective inventory placement all along the supply chain and decreases operating costs, such as production, transportation, and administrative expenses. Supply Chain optimization frequently involves using mathematical modeling approaches in conjunction with computer software.
Decision-making strategies for supply Chain optimization
Regardless of their complexity, the impact of socio-economic trends and market dynamics on supply chains stresses the need for companies to respond to a demand-driven environment from the outside in. The business world is now faced with a new set of macroeconomic issues. As a result, many companies are forced to review their business continuity strategies, for example, moving distribution centers or manufacturing facilities to another country or shifting supplier base nearer to assembly plants.
Strategy 1: Use real-time demand data to drive business planning and operation
As supply chain management teams use more powerful digital technologies, demand-prediction capabilities continue to mature. Supply chain management teams can easily change their supply chains to fit predicted demand based on real-time insights using artificial intelligence and the Internet of Things (IoT) via cloud deployments. It allows businesses to establish unified data models supplemented by external sources since it will enable them to migrate their data and applications. As a result, planning accuracy and predictive power have reached a level that was impossible before.
Strategy 2: Develop an agile, flexible, and integrated supply chain
When it comes to supply-chain planning, agility is the buzzword. Synchronizing planning and manufacturing is becoming even more prevalent among businesses, resulting in faster and more flexible operations. Implementing integrated planning in real-time, though challenging due to enormous data; financial, material planning, and business execution activities, can be connected via cloud-based solutions.
Strategy 3: Optimize product version development for supply, production, and sustainability by using constraint management
Almost every high-tech product is getting launched in a new version every year. To accomplish this, supply chain planners and design teams are increasingly being integrated into a single cloud-based platform. Product developers use collaborative tools to get inputs from planners who can create an optimization model using constraint-based supply chain planning.
Constraint-based supply chain planning
Constraint-based supply chain planning aims to provide an ideal time-phased replenishment plan for all items/ locations to accomplish targeted customer service while adhering to inventory policies and real-world restrictions at all levels of the supply chain. Supply chain limitations, supply chain status, and business rules are all inputs to restricted supply planning. Constrained planning generates supply chain KPIs, exception warnings, feasible plans, planned purchase orders, transfer orders, production orders, and VMI orders needed to carry out the plan.
Constraint-based supply chain planning is critical because it provides a plausible plan that you can implement. When establishing an optimal supply chain plan, various constraints must be considered, including supplier constraints like order minimums and maximums, as well as production capacities of suppliers; manufacturing constraints include limitations on multi-stage production, batch size limitations, capabilities, working days, and downtime hours; warehouse constraints like storage space and finally financial constraints like inventory value or even cash flow if business demands it.
Developing and maintaining a full constraint-based supply chain planning capacity takes time and effort. It is preferable to start modestly and work up to more advanced scenarios. Most businesses that develop constraint-based planning capabilities already have functional demand planning and inventory planning. Many will also take the intermediary step of developing an unconstrained planning capacity before proceeding with constraint-based planning.
Simulation modeling is used in various industries to enable developers and users to describe a system and evaluate its functioning under various dynamic 'What-if' scenarios, like changing weather or geopolitical issues, without disrupting the operational system. As a result, simulation modeling can be used as an analysis tool for forecasting the consequences of changes to existing systems or as a design tool to predict the performance of new systems under varied sets of input parameters or situations. As a result, it aids in lowering the cost, hazards, and superfluous human efforts if similar tests are carried out in the actual world.
Involvement in simulation modeling development helps decision-makers concerned gain a greater awareness of the problems they face and new perspectives on the relationship between the system's parts of interest and the measurements of its effectiveness.
Shedding some light on linear programming and its use in optimization
Operations research, a subfield of applied mathematics also known as decision science, employs various optimization techniques to aid decision-making in the face of highly complex issues. These highly complicated decision-making problems are frequently solved using linear programming. Linear programming is a mathematical modeling technique that can allocate limited resources like materials, equipment, and so on to numerous competing activities.
A typical linear programming problem consists of a linear objective function that must be maximized or minimized while constrained by a finite number of linear constraints. A simple example we have learned in school:
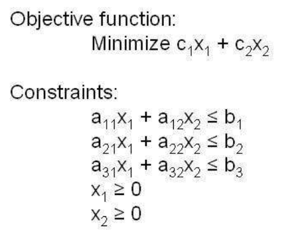
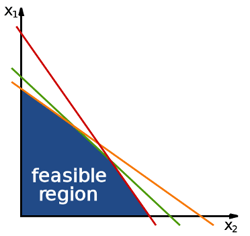
Expanding the above example to hundreds or thousands of constraints can replicate complex supply chains. Planning software in the market like o9 or Blue Yonder has heuristics solvers who can optimize real-time changes in demand and create schedules. These changes and cumulative results can be directly linked to AIOimpact from aioneers.
Example: Use of optimized inventory with resource hours in healthcare supply chain management
An inventory-oriented strategy ensures adequate inventory levels but ignores human resource operations. However, supply chain managers in healthcare require solutions to several issues other than inventory control, such as those concerning the planning, management, and scheduling of activities and labor resources. When should each employee work? When and how often should each care unit (CU) be replenished/visited? When and how often should you contact suppliers?
Further, with an inventory-oriented approach, all choices are centered on cost or service levels and do not consider other advantageous elements associated with activity control.
In the hospital supply chain management, manpower resources are needed to complete four major activities:
(1) procurement and purchase;
(2) reception and handling;
(3) replenishment preparation;
(4) distribution and inventory management at care units.
The suggested model aims to aid supply chain management optimization by giving a method for scheduling and coordinating these actions while keeping inventory costs and capabilities in mind.
The method is based on two modeling approaches that account for the supply chain managers' many scheduling decisions. The first model, M1, is an inventory cost-oriented model to minimize overall inventory costs. Each product is assigned a utility function (stock value) that accounts for its price, volume, weight, and demand variation. This model maximizes visits to the care units by reducing the stock value function. This means hospitals should order more often and keep stock levels in central shops at a minimum. The model also recommends regulating inventory levels in care units by assigning someone to make replenishment choices.
The second model, M2, attempts to establish a schedule of activities that balance the effort throughout the weekdays. M2's goal is to reduce overall resource hours for all supply chain management staff throughout an operation. Together, M1 and M2 outputs provide substantial information correlating inventory costs and the number of resource hours per day divided across supply chain management operations.
In healthcare, it is paramount to make the right decisions as low service levels result in people not getting treated or even dying. Optimization in healthcare supply chain management tackles the broad challenge of supplying products to consumers at the optimal overall cost and offering the best service.
Conclusion
The use of technology, advanced forecasting algorithms, or simulation modeling via constraints makes executive decisions a lot less risky and can show huge benefits resulting in immediate improvements on the bottom line. But after decision support comes execution management. Execution management systems can support you in acting on executive decisions. Our digital execution management system AIOimpact enables you to track optimization initiatives on the SKU level. Track every 'what if' scenario from inception until the end of the supply chain and keep the business running on time, even when conditions are less than ideal.
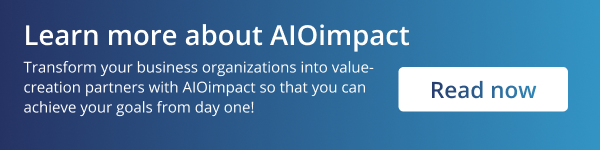